Construction Cost Estimating Methods
A construction cost estimating method is a way to predict a project's cost. The various methods, such as analogous, parametric, and bottom-up estimating, take a unique approach (such as comparing previous projects or detailing the tasks) and are intended for different stages and to balance speed, accuracy, and detail.
It’s important to distinguish these methods from types of construction estimates, which categorize estimates by their purpose or timing. For example, a feasibility estimate might use parametric estimating, while a bid estimate might rely on bottom-up calculations. To explore estimating types in detail, see our companion article on how to write a construction estimate.
In this article, we’ll focus on the methods themselves. You’ll learn how to choose the right one for each project and project phase. Then we detail each main method, including benefits, challenges, and when to use it.
Learn how to write a construction proposal in our article of free construction proposal templates.
Analogous Estimating
Analogous estimating is a construction cost estimating method that relies on learning from the past. This method requires you to take the cost of a similar, completed project and use it as a baseline for your current project. Make adjustments for key differences such as size, materials, or complexity. It’s quick and practical, especially when you’re just starting out and need only a rough number.
The key to this method is knowing your projects well enough to spot meaningful similarities and differences, so the estimate is not just a shot in the dark.
- Benefits: Saves time and builds on real-world experience; great for early-stage estimating.
- Challenges: Relies on having comparable projects and solid data. When the differences are significant, the estimate isn’t very accurate or useful.
- When to Use: Early in a project, when details are limited but you need a ballpark figure to guide planning or discussions.
Pro Tip: “For analogous estimation, stick to similar projects in the same area,” says Aaron Lipman, owner of Two Brothers Foundation Repair, a Houston-based construction company. “In Houston, I know the soil in one neighborhood might behave completely differently from another, even a few miles away. Using past jobs in the same area gives me a baseline that’s usually spot-on.”
Parametric Estimating
Parametric estimating uses measurable factors — such as cost per square foot or labor hours per unit — to calculate an estimated total project cost. This method is about identifying the key parameters that drive costs and applying them consistently across projects. If you have good data and a clear understanding of your project, this method can give you a more precise estimate without requiring you to have every detail nailed down.
- Benefits: Brings structure and accuracy to estimating; is scalable to different project sizes or scopes.
- Challenges: Requires solid, up-to-date data; you must also have a strong handle on what drives costs for your specific job.
- When to Use: When you know the key metrics for your project and need a more refined estimate than a general comparison.
- Useful Tool: Download this parametric cost estimating template in Excel , Microsoft Word , or Smartsheet formats.
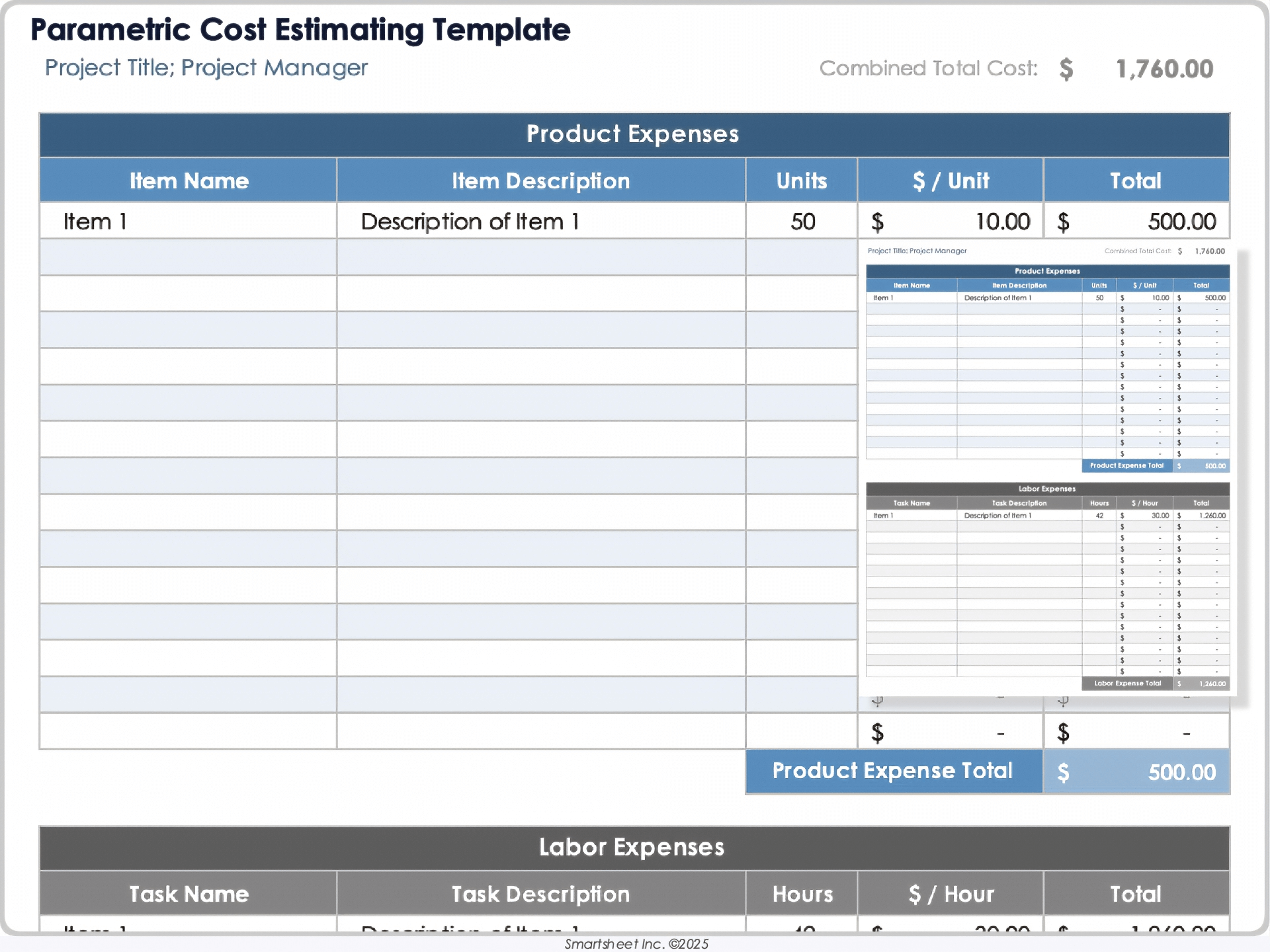
Pro Tip: Don’t rely solely on formulas. “Parametric estimating, like using cost-per-square-foot, is great for quick ballpark figures, but real-life variables can mess with it,” says Brendan Anderson, a second-generation roofer and owner of Brix Systems Roofing in Kalispell, Montana. “For example, after a storm, prices for shingles and supplies shot up in my area, and my parametric estimates fell short. I learned to combine it with local knowledge to get a more accurate number.”
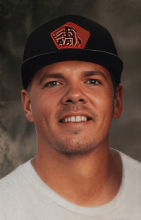
Bottom-Up Estimating
In bottom-up estimating, you break the project into individual tasks or components, estimate the cost of each one, and then add it all together to find the total estimate. It is more time-intensive, but typically results in the greatest accuracy. If precision is your goal and you have a well-defined scope, this should be your go-to method.
- Benefits: Provides crystal-clear insight into where your money is going, per task or component.
- Challenges: It’s a time commitment, and you’ll need to know the specifics of every task and resource.
- When to Use: When your project plan is solid and you’re ready for a detailed budget.
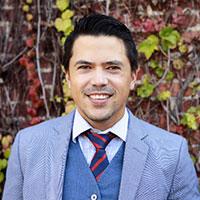
Pro Tip: Bottom-up estimating has great benefits if you have the time and details. “We take a bottom-up approach to creating our cost estimates,” says Jared Malapit, certified estimating professional and Principal at Precision Estimating Services. “This allows us to think through the project in detail and pass that understanding along to our clients, [which allows] them to understand not only how much their projects should cost, but also why and what opportunities may be available for value engineering the design.”
Check out our roundup of free construction scope of work templates to learn how to define your project’s scope.
Three-Point Estimating
Three-point estimating uses three scenarios — best case, worst case, and most likely — to calculate the estimated range of total costs. It’s like creating a safety net for your estimate by factoring in uncertainty and risk. This method works especially well if you’re dealing with unpredictable variables or projects with a lot of unknowns.
- Benefits: Helps you plan for surprises by including both optimistic and cautious scenarios.
- Challenges: Requires thoughtful scenario-building to be useful; can feel abstract without experience.
- When to Use: When there’s a lot of uncertainty, and you need a plan that accounts for risks.
- Useful Tool: Download and use this three-point cost estimating template available in Excel .
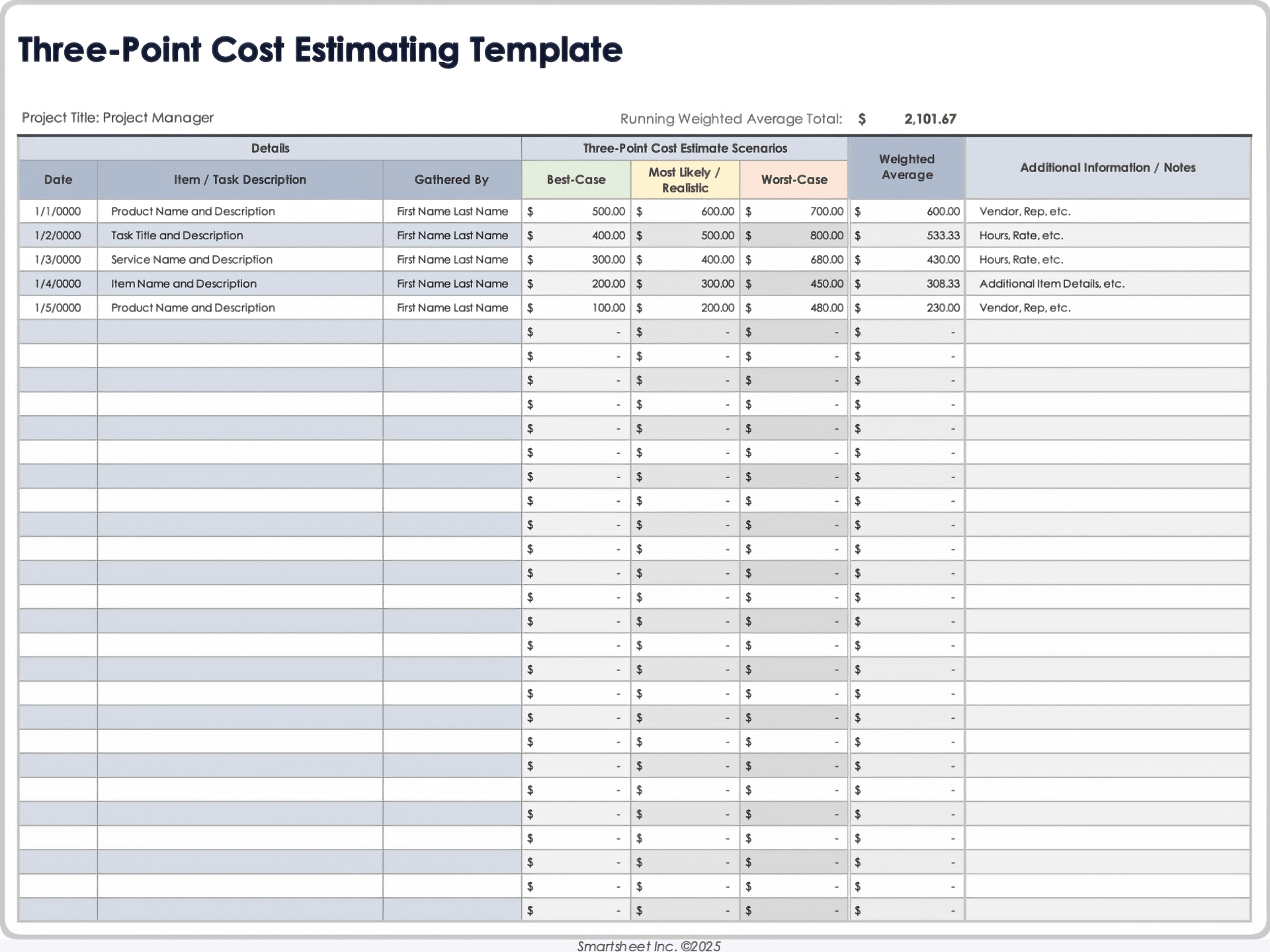
Expert Judgment
Expert judgment relies on the experience and intuition of seasoned professionals to come up with an estimate. It’s fast, flexible, and perfect for one-of-a-kind projects. But because it’s subjective, it works best when paired with other methods or backed by data.
- Benefits: Quick and adaptable; brings valuable expertise to the table.
- Challenges: It’s only as good as the expert providing it, meaning biases and blind spots can creep in.
- When to Use: When tackling a new or unconventional project, or when you’re short on data.
Resource-Based Estimating
Resource-based estimating zooms in on the resources: the materials, labor, equipment, and fees that your project requires. Calculate the cost of each resource and add them together to get a detailed estimate. It’s particularly effective when you have a clear idea of what and how much you’ll need.
- Benefits: Gives you a granular view of costs, which will help you manage resources better.
- Challenges: You’ll need accurate resource plans, and pricing fluctuations can throw things off.
- When to Use: When resource requirements are well-defined, and you’re focused on cost control.
Historical Data Estimating
Historical data estimating is all about pulling cost information from past projects and using it to guide your current ones. Unlike analogous estimating, which compares your project to one specific past job, this method uses multiple projects — and therefore, a broader data set — to identify patterns. You might pull average material costs, crew productivity, or equipment expenses from your project history and adjust for inflation, location, or other factors.
- Benefits: Builds on a large pool of real-world data from multiple projects, which makes it reliable for standardized or recurring projects.
- Challenges: Requires well-maintained records and careful adjustments to fit the specifics of your current project.
- When to Use: For projects with repetitive elements or similar scopes, where past data can reveal useful patterns.

Pro Tip: Be aware of the limits of historical data estimating. “In estimates during the planning and design process, I believe most mistakes are made by relying on historical data only without looking at the specific needs, wants, and constraints of the current project,” explains Marcene Taylor, President of the construction estimating firm Marcene Taylor Inc. and former President of the American Society of Professional Estimators, an organization that represents construction estimators.
Production Rate Estimating
Production rate estimating takes a practical look at how fast crews and machines can work. Whether it’s the number of square feet painted per hour or the amount of concrete poured in a day, this method allows you to calculate labor and equipment costs based on actual performance. It’s great for estimating the labor costs of tasks you’ve done many times in the past and for which you have reliable productivity data.
- Benefits: Makes use of real-world numbers, so it’s dependable for routine tasks.
- Challenges: Productivity can vary depending on site conditions, weather, or crew skill levels.
- When to Use: For repetitive work where you have consistent data on crew or equipment output.
Capacity Cost Factoring
Use capacity cost factoring to scale industrial or manufacturing projects. It accounts for economies of scale, where doubling capacity doesn’t necessarily double costs. For example, expanding a factory might still mean using the same utilities, which reduces the per-unit cost. This method uses a multiplier — such as the six-tenths rule — to estimate how costs change as you scale up.
- Benefits: Captures economies of scale; ideal for feasibility studies in industrial projects.
- Challenges: Limited to large-scale projects, such as a manufacturing or storage facility expansion; requires strong historical data for calibration.
- When to Use: During early-stage feasibility analysis for manufacturing plants or similar facilities.
Model-Based Estimating
Model-based estimating uses advanced 3D models with building information modeling (BIM) software. This method produces a detailed estimate from the design, with both material quantities and cost.
- Benefits: Increases accuracy by putting together design and pricing data; helps reveal scope gaps or design errors.
- Challenges: Requires software expertise; creating the model can take extra time and effort.
- When to Use: On large, complex projects where the design is well-developed and accuracy is critical.
Probabilistic Estimating (Monte Carlo Simulation)
Probabilistic estimating, also called a Monte Carlo simulation, is great when you want to tackle project what-if scenarios. Instead of giving you only one number, the method provides a range of possible costs by running multiple scenarios.
- Benefits: Helps you understand best- and worst-case scenarios, not only the middle ground.
- Challenges: Requires some technical know-how to set up and interpret, plus software to run.
- When to Use: For projects with a lot of unknowns, such as those involving new methods or high risk.
Delphi Method
The Delphi method gathers a group of experts to provide cost estimates, refining their numbers over several rounds until they reach consensus. They share their estimates anonymously and compare each other’s insights. It’s a collaborative way to build a reliable estimate for projects with high uncertainty or where no clear precedent exists.
- Benefits: Uses expert consensus to improve accuracy; great for complex projects with unknowns.
- Challenges: Time-consuming and requires access to a qualified group of experts.
- When to Use: Unusual or high-stakes projects with uncertainties.
Value Engineering
Value engineering is about finding smarter ways to hit your goals without spending more than you need to. For example, you might save costs by switching to a different material, reworking a design, or rethinking a method — it’s all about finding ways to get the same quality for less. This approach works best as a team effort, with everyone from designers to builders pitching ideas.
- Benefits: Encourages creative problem-solving and can lead to big savings.
- Challenges: Requires time and cooperation, and not all suggestions will work.
- When to Use: When you’re in the design phase and want to make every dollar count.
Modular Estimating
If your project has repetitive sections or uses prefabricated parts, modular estimating is the way to go. In this method, you divvy up the project into parts, estimate the cost of each, and add it all up. For example, you might calculate the price of one modular unit and scale it across the entire building.
- Benefits: Ideal for prefab or repetitive builds; simplifies estimating complex projects.
- Challenges: Can miss how modules interact or overlook site-specific costs.
- When to Use: For modular construction or projects with repeatable elements.
Lifecycle Cost Analysis
You can use lifecycle cost analysis (LCCA) to look beyond the initial price tag to what a project will cost over its entire lifespan. LCCA considers factors such as maintenance, operations, and even replacement costs. This method is especially valuable for public buildings, roads, or bridges.
- Benefits: Gives a full picture of costs, helping you make smarter long-term decisions.
- Challenges: Hard to predict future costs.
- When to Use: For projects with high ongoing costs, such as infrastructure or facilities with long lifespans.
Ratio Estimating
Ratio estimating breaks down a project’s costs into broad categories, such as labor, materials, and equipment, and assigns percentages to each. For example, you could estimate that labor will take up 40 percent of the budget while materials are 30 percent. It’s a quick way to divvy up costs and can be helpful for planning when you don’t need exact numbers yet.
- Benefits: Simple to use; helps with high-level budgeting.
- Challenges: More of a rough guide; lacks details.
- When to Use: Early on, when you need a broad overview of where the money will go.
How to Choose the Right Construction Cost-Estimating Method for Your Project
Picking the best way to estimate costs doesn’t have to feel like guesswork. It’s all about matching your method to the project stage, your goals, and the level of detail you have to work with. Follow these steps to make your choice.
1. Determine What You’re Trying to Achieve
Ask yourself what you’re aiming to accomplish with the estimate. Are you making an early go-or-no-go decision, setting a project budget, or preparing a detailed bid? For example, quick options such as analogous estimating make sense for feasibility studies. Detailed bids, on the other hand, need more precise techniques, such as bottom-up estimating.
2. Start With What You Know
The amount of information you have is crucial. If your plans are still high-level, you’ll want to stick with methods that don’t rely on specifics. Once your project is more fleshed out, you can move to approaches that dig into details.
3. Match the Scale and Complexity
Think about your project’s size and intricacy. A simple renovation doesn’t need advanced tools, but a large, multi-phase build does. Tailor your method to suit what you’re working on.
4. Look at Your Timeline
How much time do you have to prepare the estimate? Faster methods, such as parametric estimating, work when deadlines are tight. If you have more time, you can explore detailed approaches to get a closer estimate.
5. Decide How Accurate You Need to Be
Not all estimates need to hit the same precision level. Early-stage planning can tolerate rough numbers, while later phases — such as construction or bidding — require detailed and accurate estimates.
6. Plan for Surprises
When there are unknowns, such as fluctuating prices or unpredictable conditions, make sure your estimate accounts for them. Using three-point estimating or other risk-focused methods can help.
7. Mix and Match Methods
You don’t have to stick to only one approach. Use a broad method, such as parametric estimating, to establish a foundation. Then refine it with a more detailed approach for key areas.
8. Test on a Small Scale
Before committing, try your method on a smaller piece of the project. This lets you see if it works and gives you a chance to make adjustments early.
Every project is different, and the more estimates you prepare, the better you’ll get at finding a method that works for each situation. Whether you need speed, detail, or flexibility, you can find an approach that fits your needs.
CONSTRUCTION COST ESTIMATING METHOD | WHEN TO USE |
---|---|
Analogous Estimating | Early project stages for a quick ballpark figure with limited details |
Parametric Estimating | When key metrics such as cost per unit are known and moderate accuracy is needed |
Bottom-Up Estimating | For detailed project budgets when scope and specifics are well-defined |
Three-Point Estimating | When you have many uncertainties or risks to account for multiple scenarios |
Expert Judgment | For unique projects, especially when data is scarce |
Resource-Based Estimating | When resource requirements are clear and granular cost management is needed |
Historical Data Estimating | For projects with repetitive elements or where past project data is reliable |
Production Rate Estimating | For routine tasks with consistent productivity data like labor or equipment output |
Capacity Cost Factoring | During feasibility studies for industrial or manufacturing projects scaling capacity |
Model-Based Estimating (BIM) | For large, complex projects requiring integration of design and cost data |
Probabilistic Estimating | For projects with high uncertainty, leveraging scenarios to explore cost ranges |
Delphi Method | For novel or high-stakes projects, relying on collective expertise for accuracy |
Value Engineering | During the design phase to find cost-saving opportunities without compromising quality |
Modular Estimating | For modular or prefabricated construction projects with repeatable elements |
Lifecycle Cost Analysis (LCCA) | For projects where long-term costs such as maintenance and operation are critical |
Ratio Estimating | During early planning for a broad breakdown of costs into major categories |
For additional templates for your construction project, check out our roundups of free construction budget templates and free construction estimate templates.
Download the Cost Estimate Cheat Sheet
Get a more detailed version of the table above, including a specific example of each method and estimate types to use it on. Keep it handy as you learn the ropes of construction cost estimating methods.
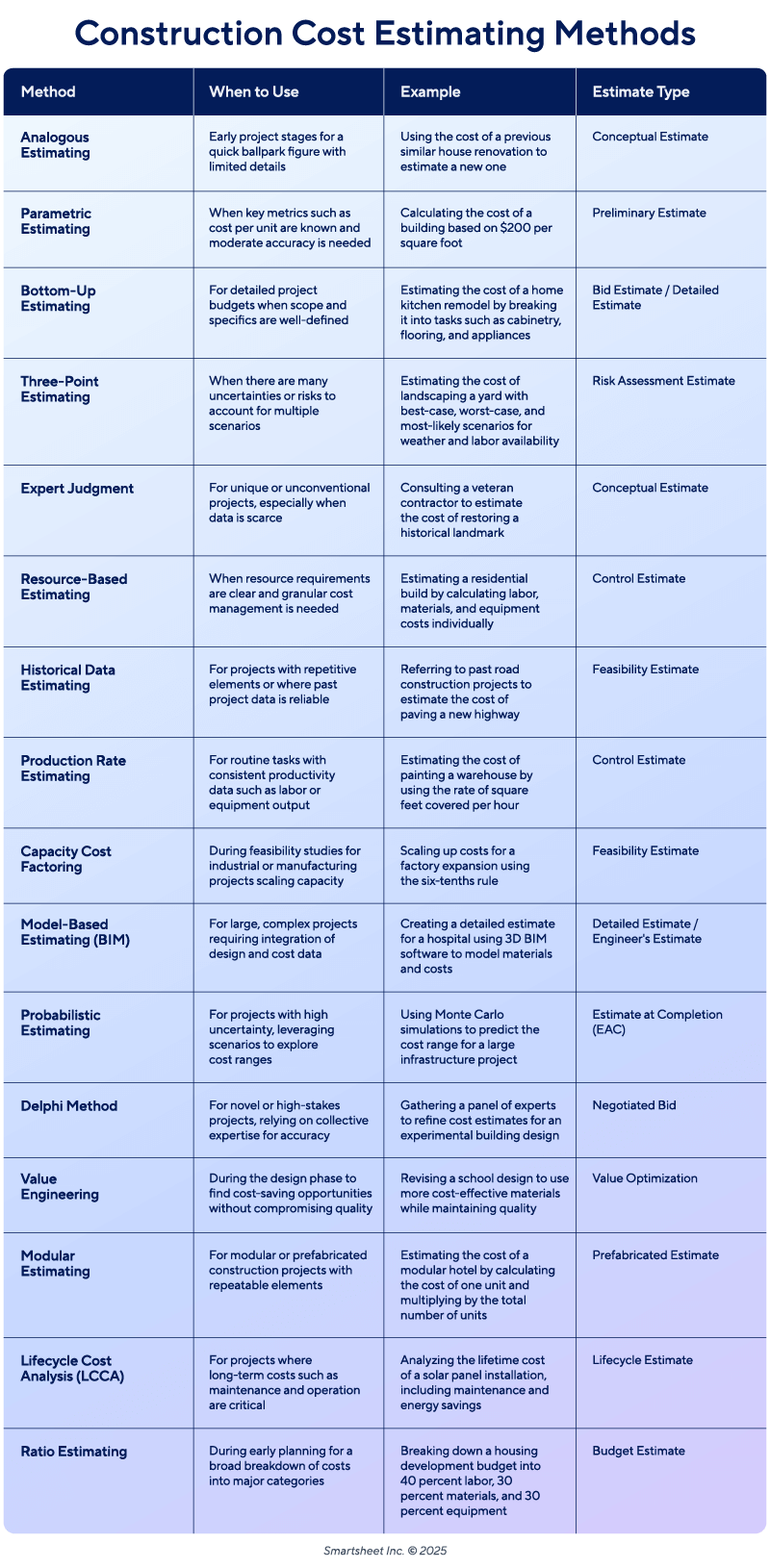
Improve Construction Cost Estimating With Smartsheet for Construction
From pre-construction to project closeout, keep all stakeholders in the loop with real-time collaboration and automated updates so you can make better, more informed decisions, all while landing your projects on time and within budget.
The Smartsheet platform makes it easy to plan, capture, manage, and report on work from anywhere, helping your team be more effective and get more done. Report on key metrics and get real-time visibility into work as it happens with roll-up reports, dashboards, and automated workflows built to keep your team connected and informed.
When teams have clarity into the work getting done, there’s no telling how much more they can accomplish in the same amount of time. Try Smartsheet for free, today.