What Is the Critical Path Method in Construction?
The critical path method (CPM) helps you figure out which tasks control when your construction project will be completed. It maps out the longest sequence of dependent work — the tasks that can’t be delayed. You can use CPM to prioritize your work and preempt delays.
Most construction projects include a mix of flexible and time-sensitive tasks. If the wrong task is delayed or disrupted, the entire schedule slips. The critical path is the sequence that sets the pace. It’s not rigid, but it is the shortest viable path to completion. CPM helps you see this path clearly and manage it intentionally.
Schedules can unravel for all kinds of reasons: permits, inspections, subcontractor conflicts, supply delays. Even a task as simple as a trench inspection can knock plans off track.
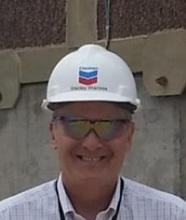
“Project management is difficult and complicated because it deals with people in the real world,” says Stanley Wanless, who worked as a master scheduler at PotashCorp (now Nutrien). “You can’t just go by what you read in a book. In the field, things don’t happen that way.”
That’s exactly why CPM is so valuable. It provides a framework to organize what needs to happen, in what order, and how each task impacts the rest of the job.
In construction project management, some tasks hold the schedule together. If framing runs late, roofing is delayed. If inspections slip, drywall gets pushed. The chain of tasks with no room to slide is your critical path.
To make that path visible, CPM breaks the project into six essential parts:
- Tasks: These are the building blocks of your project, each one representing a specific, measurable unit of work. A task might be “Excavate trench for footing” or “Rough-in electrical.” The goal is to keep each task scope small enough to schedule and track.
- Dependencies: Some tasks can’t begin until others are finished. These relationships are called dependencies. For example, you can’t start framing until the slab is poured and cured. Dependencies link tasks together in a logical sequence and define the order of operations.
- The Critical Path: This is the longest continuous chain of dependent tasks with no float. In other words, it’s the path that sets your project’s finish date. Any delay here pushes the entire schedule, unless another task is shortened.
- Float (Slack): Float is the amount of margin time that a task has for delays without affecting the end date of the project. Tasks on the critical path have zero float. Tasks with float give you flexibility and a way to shift resources without adding risk.
- Network Diagrams: These visual charts, also known as critical path diagrams, illustrate the connections between tasks. Boxes represent tasks, and arrows represent dependencies. A well-built network diagram helps you and your team see the entire sequence at a glance — and spot where things might go off track.
- Forward and Backward Passes: These calculations define early start, early finish, late start, and late finish for each task. They allow you to measure float, identify the critical path, and adjust the plan with on-site changes. They might also be used with the program evaluation and review technique (PERT), which uses optimistic, pessimistic, and most likely durations to help estimate schedules when there’s uncertainty around task timing.
In the video below, F. Lawrence Bennett, Professor Emeritus of Engineering Management, explains the critical path method using a tank installation at a construction site.
Transform construction management with Smartsheet. See for yourself.
Would you like to manage your construction projects more efficiently, get better visibility into project risks and dependencies, and optimize resource planning?
Smartsheet empowers construction teams of all sizes to improve visibility to critical information, boost collaboration across field and office teams, and increase overall efficiency, so you can deliver projects on time and on budget.
Why Contractors Use the Critical Path in Construction
Contractors use the critical path method to plan projects better, keep them on track, and manage risk. By highlighting which tasks drive the finish date, CPM helps teams stay focused, avoid delays, and make better use of labor, equipment, and materials, even on complex jobs.
Despite its importance, CPM doesn’t always get the investment or attention it deserves.
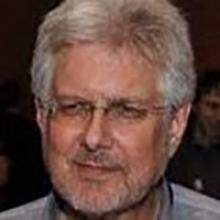
“Pretty much every contractor has an estimating department, but almost none has a scheduling department,” says Chris Carson, Vice President at ARCADIS U.S. and co-author of CPM Scheduling for Construction: Best Practices and Guidelines. “Estimating is where you win work. Scheduling is where you ensure the work is done on time and profitably.”
CPM is part of most formal training programs, including PMP certification, but applying it effectively in the field requires more than just coursework. Critical path planning isn’t only about hitting deadlines: It helps teams control costs, avoid confusion, and make better decisions, especially when things don’t go according to plan.
The critical path method cuts through the chaos. Construction projects are notoriously complex, often involving dozens of crews, overlapping tasks, and tight deadlines. CPM helps teams figure out which steps truly control the schedule, so they can focus their attention where it matters most. It’s the difference between guessing and knowing whether the drywallers can start or if they need to wait for the framers to finish.
CPM also brings order to logistics. For example, when a long-lead item such as custom glass is on the critical path, that tells the team to get the order in early. When a crane is needed for a task with no wiggle room, it gets booked first. Instead of scrambling to react, teams can plan ahead with confidence.
Once the schedule is mapped out, contractors can look for smart ways to shave time, such as overlapping certain phases (fast-tracking) or adding more crews to speed up a task (crashing). But those strategies only work if you have a clear picture of what depends on what. That’s what the critical path method provides.
CPM also offers practical solutions for contracts and disputes in construction. Many owners require a CPM schedule up front, which can be used to identify ownership and responsibility if delays occur. Courts and claims consultants often use the critical path to assess damages.
The critical path method is baked into the way that bigger firms run major projects. It helps close the gap between the office and the jobsite, especially as scheduling tools become easier to use in the field.
How to Make a Critical Path Construction Schedule
To build a critical path schedule, break down your project into tasks. Figure out how the tasks are connected and estimate how long each takes. Finally, map out the chain that drives your finish date. This is your critical path, which tells you exactly where a delay hurts most.
Here are the steps to creating a critical path construction schedule:
1. List Every Task That Needs to Happen
Start by breaking your construction project into clear, manageable parts. A construction work breakdown structure (WBS) helps you organize everything that needs to happen, phase by phase, before you start estimating durations or setting dependencies.
Instead of showing task order or timing, a WBS lays out the scope of work in a structured, hierarchical list. You might group tasks under categories such as Site Work, Framing, or MEP Systems, and assign codes (e.g., 1.0, 1.1) to help track them later in your schedule.
Once you build your WBS, you’ll have a complete task list to feed into your critical path schedule.
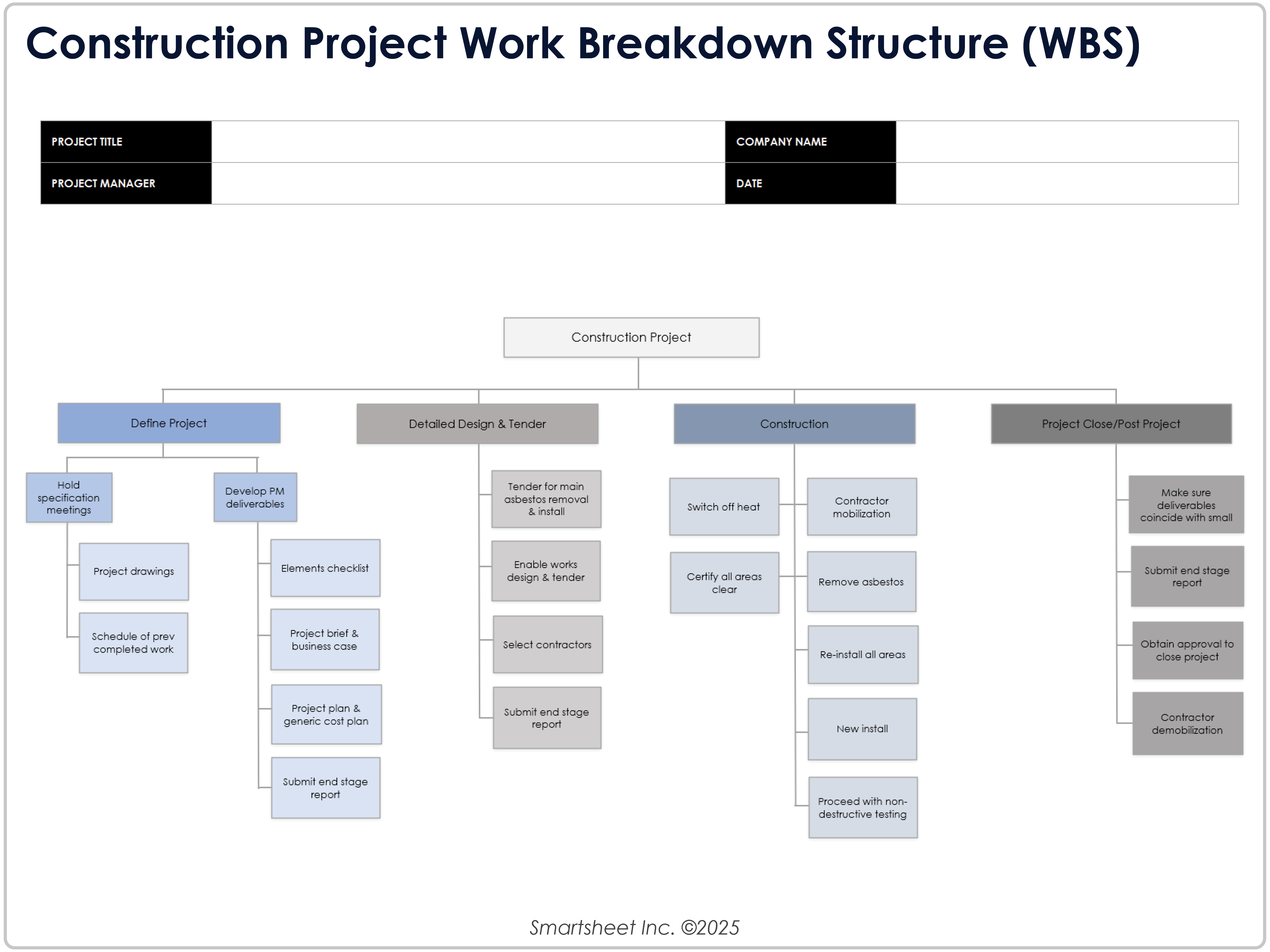
Download the Construction Project Work Breakdown Structure (WBS) Template for Excel
2. Note Predecessor-Successor Links (Dependencies)
For each activity, ask: What needs to happen before this task can commence? Some tasks rely on others (e.g., you cannot start drywall until inspections are complete), while others can occur independently.
Mark these as predecessor-successor links — for example, “Task 3 depends on Task 1 and Task 2.” Most CPM tools let you link tasks using ID codes or drop-downs. If you’re working in Excel or on paper, note the IDs of the prerequisite items in a separate column labeled Predecessors, as shown in the CPM construction template we provide below.
There are four varieties of dependencies:
- Finish-to-Start (FS): Task B begins after Task A finishes (most common).
- Start-to-Start (SS): Task B can kick off once Task A starts.
- Finish-to-Finish (FF): Task B must wind up when Task A finishes.
- Start-to-Finish (SF): Task B must be completed before Task A starts (rare).
Most construction schedules use FS and SS relationships. Keep the dependency logic simple.
3. Estimate Task Times
Use past experience, supplier timelines, or crew availability to set realistic time frames. If you’re not sure, ask your subcontractors or field team. Your schedule will only be as good as these estimates. Local experience is useful — it can improve predictions about factors such as weather, material lead times, available workers, and local workflow norms. Talk to supervisors on similar local jobs.
4. Build a Critical Path Diagram
A critical path diagram, also called a network diagram or activity-on-node chart, shows how tasks are connected based on dependencies. It’s a useful visual tool for mapping dependencies before building a full schedule or entering data into software.
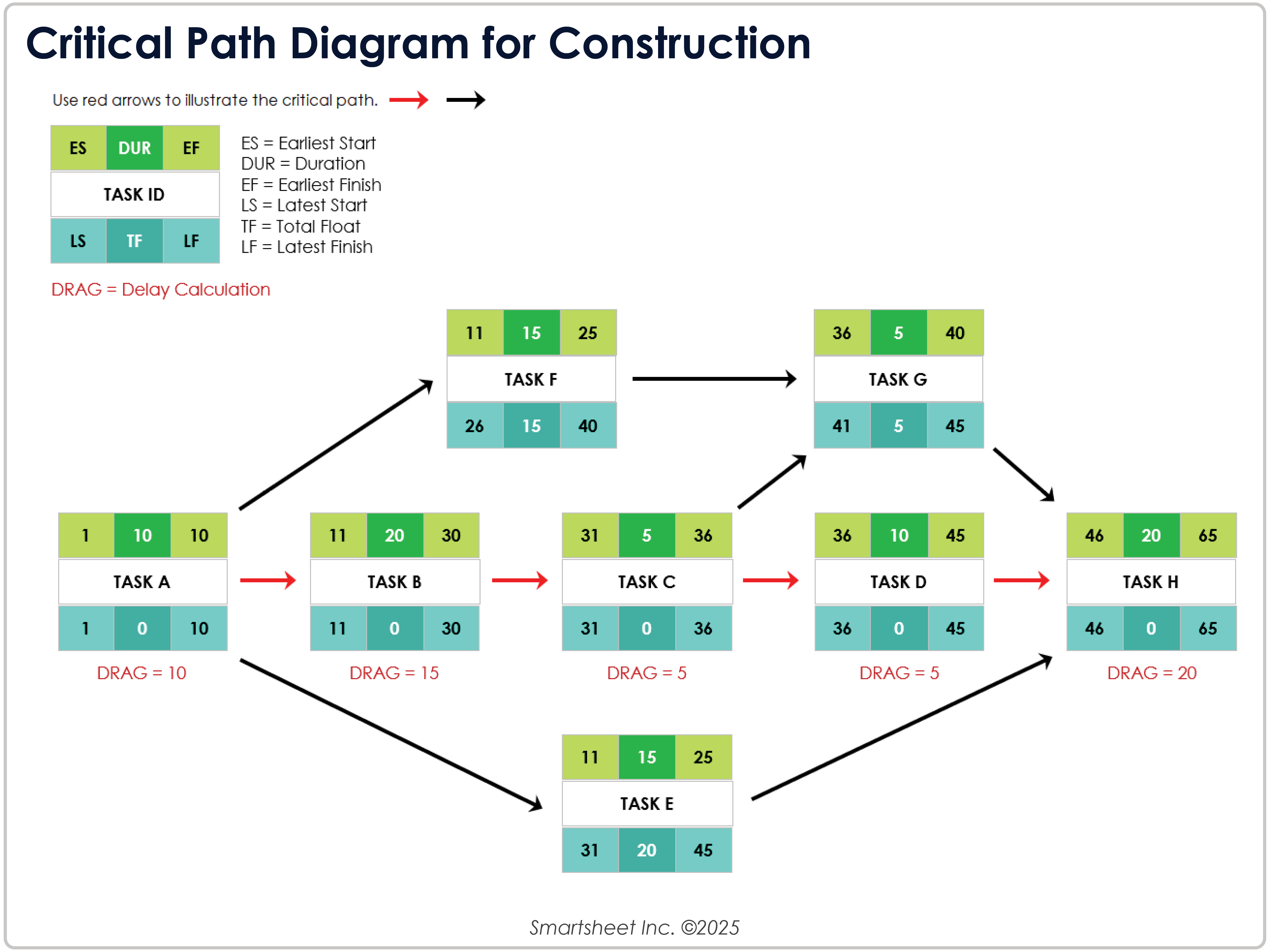
Download a Sample Critical Path Diagram for Construction for Excel
For critical path examples, check out this collection of sample diagrams from real-world scenarios.
5. Run the Forward and Backward Pass
To highlight which tasks are truly critical, you need to calculate the earliest and latest possible start and finish times for each one. That’s where the forward and backward passes come in.
The forward pass moves through your task list from start to finish, calculating the earliest start (ES) and earliest finish (EF) for each task based on its duration and dependencies. The backward pass goes from finish to start, calculating the latest start (LS) and latest finish (LF) times each task can have without delaying the project.
Once you’ve run both passes, you can calculate float (also called slack) for every task:
Float = LS − ES
Or:
Float = LF − EF
Tasks with zero float are on the critical path. They have no room to shift without pushing back the entire schedule.
Most CPM scheduling tools do this math for you automatically. But understanding the logic behind the calculations helps you catch flaws or tight spots in the schedule and keep your project realistic.
6. Plot the Schedule on a Gantt Chart
A Gantt chart turns your task list into a timeline. Software will often highlight critical path tasks in a different color, helping your team see what matters most at a glance.
Try Creating a Simple Critical Path Chart by Hand
If you’re new to critical path scheduling, sketching it out manually can help you better understand the underlying logic.
Start by listing tasks from your work breakdown structure down the left side of a page. Use the horizontal axis to represent time, marked in days or weeks. For each task, draw a horizontal bar that starts on the day the work begins and stretches across its estimated duration.
If one task depends on another, place its bar to the right of the first, leaving a space between them and using a vertical connector to make the dependency clear. For tasks that happen at the same time, stack the bars above or below each other.
Once you’ve laid out everything, look for the longest connected sequence of tasks — that’s your critical path. You can check your math by adding up the durations along each path.
This exercise won’t replace a full scheduling tool, but it’s a great way to see how task logic and timing come together to drive your project’s timeline.
Here’s what a simple, hand-drawn CPM chart might look like in practice:

When to Use CPM in Construction Management
Use the critical path method when your project has moving parts that need to stay tightly coordinated. If a delay in one area could cause a domino effect or if you’re managing overlapping crews, long-lead items, or firm deadlines, CPM gives you the structure to plan and adapt effectively.
You don’t need a full CPM schedule for every job. For a one-day repair or a simple driveway pour, a checklist and timeline might be enough. But once the project involves dozens of tasks, multiple subcontractors, or phased inspections and permits, it’s time to build a CPM schedule.
Here are the most common signs that CPM will help:
- Hard Deadlines: If the project has an external deadline — an opening, late penalties, or other dependent projects — knowing the critical path helps you plan backward and avoid bottlenecks.
- Complex Dependencies: If certain work can’t begin until multiple other steps are complete or if several tasks have to be sequenced just right, CPM helps you see those relationships clearly.
- Heavy Resource Coordination: For projects that require shared labor, limited equipment, or staggered deliveries, CPM helps schedule resources without conflict.
- Owner or Contract Requirements: Some clients, especially on public or large-scale jobs, require a formal CPM schedule before work begins. These schedules often become part of how progress is tracked or payments are approved.
You can build a CPM schedule during preconstruction and hone it as details come into focus. Many contractors use a rolling wave approach — laying out the early phases in detail while keeping later phases more flexible until they get closer. The key is starting early enough to flag problems before they’re baked into the timeline.
If you’re unsure whether a project needs CPM, ask yourself: If one task slips, do I know exactly what else it throws off? If the answer is no, then it’s time to build the schedule that will tell you.
Challenges of the Critical Path Method
The critical path method can give you great insight into your schedule, but it takes time, focus, and consistency to build and keep up. It requires frequent updates, but risks overcomplicating a project; the critical path often shifts; and CPM tools can give a false sense of control.
Here are some challenges that you might encounter when using the critical path method:
- Inaccurate Estimates: A CPM schedule depends on realistic task durations and clear logical flow between activities. If the estimates are off or if dependencies are incomplete, the critical path won’t reflect reality. That can lead teams to prioritize the wrong tasks or miss early warnings of delay.
- Outdated Schedules: Treating the CPM plan as a one-time deliverable — instead of a living document — is a common failure. If the framing crew runs late or weather delays roofing, the critical path may shift. The schedule must be updated regularly, or it loses value.“One of the biggest mistakes I see is using CPM as if it were a one-and-done planning tool,” says Yogesh Choudhary, Co-Founder and CEO of FieldCircle, which advises field service and construction teams. “But construction and field work never go 100 percent according to plan. The more effective approach is to treat CPM as a living document — syncing it with field reality, not just project theory.”
If you don’t review the critical path frequently, tasks that were once flexible can become schedule blockers.
- Static Critical Path: Some teams treat the critical path as fixed, but it can shift with any change in task duration, sequencing, or resource allocation.
“A common mistake I see contractors and project managers make when using the critical path method is underestimating how flexible the critical path can be,” says Todd Stephenson, Co-Founder of Roof Quotes, a roofing marketplace that creates a blueprint and detailed scope of work for homeowners’ roofs.
“Many people treat the critical path like it’s set in stone, but that’s not the case,” he says. “The key to using CPM effectively is recognizing that it is dynamic. A shift in task durations, delays, or even resource changes can create a ripple effect that changes which tasks are truly critical.”
- Too Much Detail: Especially on large builds, it’s easy to overcomplicate the plan. Thousands of activities, overmodeled logic, or forced precision can make the schedule unreadable to the people who need it most. Many field supervisors still prefer short-term, practical plans over what they see as bloated formal schedules.
“I’ve seen 500-line schedules that no one reads,” says Drew Wiard, who manages home builds and repairs and owns Clear Sky Properties in Indiana. “Crews ignore them, subs miss updates, and everything falls apart. A schedule should guide the job, not control it.”
- Poor Integration: A scheduler might build a rock-solid CPM plan, but if it’s not integrated into how the field runs day to day, it won’t help. When crews and foremen don’t reference the schedule or when project managers treat it as a paper exercise, the critical path becomes meaningless.
- Overdependence on Software: Tools can automatically calculate float, draw Gantt charts, and highlight critical tasks. But if the logic is wrong or the data is stale, software can give a false sense of control.
“The most useful skill I’ve learned didn’t come from software,” says Robert Grunnah, Owner of Austin House Buyer, who has overseen dozens of home rebuilds in Texas. “It came from walking [through] a site and seeing what’s about to go wrong. If a supplier’s truck is late or a subcontractor doesn’t show, the critical path shifts in real time. If you wait for the weekly report, you’re already behind. That’s what no one tells you.”
- Default Resource Limits: A CPM schedule might show two critical tasks running in parallel, but if both require the same crew or crane, it’s not feasible to carry out these tasks according to the schedule. Without resource-leveling features or human oversight, the schedule may not reflect a real plan.
Despite these challenges, construction teams can still manage timelines effectively with CPM, as long as they build it on good data, keep it current, and use it consistently on the ground.
Critical Path Method Best Practices
To get the most out of CPM, treat the schedule as a live management tool — not just a planning formality. A well-built critical path schedule helps you stay ahead of problems, but only if it’s kept accurate, visible, and aligned with how the field actually works.
Here’s how experienced construction managers keep CPM effective:
- Keep the Schedule Current: CPM only works if the data is fresh. Update progress regularly — weekly on active jobs — and recalculate the critical path each time. Delays, weather, scope changes, and inspection timing can all shift the path.
- Look Beyond the Path Itself: Tasks with float can still turn critical if they’re neglected or delayed enough. Watch the near-critical path too — activities with very little slack may be one slip away from becoming your biggest risk.
- Collaborate During Planning: Bring in field supervisors, subcontractors, and estimators when building the schedule. They’ll catch problems and overlaps that a scheduler might miss. Buy-in during planning often leads to better use of the schedule later on.
“I talk to people who can explain the process,” says Wanless, the master scheduler. “I always seek out the oldest guy on the team, and I ask lots and lots of questions. Through this process, I come up with a schedule.”
- Regularly Review Float: Use float strategically. If one team is behind on a critical task and another has room in its schedule, reassign resources as needed. CPM makes this possible — you can see where it’s safe to pull or shift help without affecting the finish date.
- Stay Flexible: Don’t try to plan every last detail up front. For long or phased jobs, build a detailed schedule for the next 30–90 days and keep future phases planned at a higher level until you get closer. Update as you go. This keeps the schedule flexible and real.
- Be Realistic: If your CPM logic says two tasks can run in parallel but they rely on the same crew or workspace, that’s not workable. Don’t let the software dictate sequencing that doesn’t match field reality. Adjust logic to reflect real constraints.
“Crews don’t need a Gantt chart. They need a heads-up, a clear task, and a reason why it matters,” Grunnah says. “I give them one thing to move the needle that day. If they hit it, the whole plan holds. Schedules should support your team, not confuse them. If no one in the field understands the plan, it’s your fault.”
- Ensure Accessibility: Post a simplified version of your schedule on-site or share it digitally so that it’s highly visible and everyone can access it. Highlight critical tasks visually. If the schedule lives only in a file on the project manager’s laptop, it won’t drive decision-making.
“To make CPM schedules work for field crews, you must take complicated CPM charts and reduce them to simple, actionable daily work plans,” says Mike Aziz of M1 Home Buyers. “Field crews don’t need Gantt charts; they need shorter lists of task dependencies and deadlines. We use mobile-optimized dashboards that update in real time, showing crews their top priorities and any variations in the critical path.”
Using a Critical Path Template for Construction
A critical path template helps you organize tasks, define dependencies, and calculate timelines. You want to do this before handing everything over to scheduling software. It’s also useful as a lightweight tool for managing smaller jobs manually.
Whether you're building your own schedule in Excel or reviewing one from a general contractor, a template makes the critical path easier to see and track. The example template we’ve created includes fields for task names, WBS codes, durations, start and finish dates, dependencies, float, and critical path flags.
Here are directions for creating a critical path schedule:
-
Download the critical path template for construction in Excel
or Google Sheets.
- Enter task names under the Task Name column. Use the WBS ID column to group and number each item. For example, 1 might be “Obtain Permits,” 1.1 “Site Prep,” 1.2 “Foundation Work,” and so on.
- Input the number of working days needed for each task under Estimated Duration. Then enter the estimated start date. The template will auto-calculate the estimated end date using the formula.
- Define dependencies in the Predecessors column by entering the WBS ID(s) of the task(s) that must be completed first. This allows the schedule logic to follow real-world sequencing. For example, if Framing can’t start until Foundation Work is done, enter 1.2 as the predecessor to 1.3.
- If known, enter the float (slack time) for each task in the Float (days) column. Float is how many days a task can be delayed without affecting the overall project finish date. If you enter 0 float, the template will automatically flag that task as part of the critical path.
- Your entries automatically create the Gantt chart.
- Use the Blank tab to build your own schedule from scratch. All logic and formulas are preserved; just fill in your own tasks and dates.
You’ll find more options in our library of downloadable critical path templates for different project types. You can also browse our collection of construction schedule templates to find formats made for specific trades, timelines, or phases.
CPM Software for Construction Project Scheduling
Even the most experienced construction teams will benefit from good software, not just to build a schedule, but to keep it accurate and actionable. A good CPM scheduling tool should help you define task logic, watch progress, see delays, and communicate with the team.
Modern software handles most CPM calculations automatically. Input your task list, durations, and dependencies, and the tool will calculate start and finish dates, float, and the critical path. Many platforms also let you adjust timelines in real time, test what-if scenarios, and generate schedule reports with a few clicks.
But not all project scheduling tools are built with construction workflows in mind. Look for features that support how your team actually works — from mobile access in the field to realistic dependency handling and resource coordination. Also, make sure you can integrate it well with your other systems.
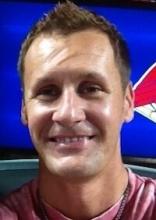
Andrew Bates, COO of Bates Electric, uses project management software to manage large-scale commercial projects.
“I use it not just to schedule, but to help the field stay focused on what matters most each week,” he says. “To make it useful, I rely heavily on activity codes to organize the schedule by trade, location, and priority. I assign custom codes that group related tasks, then filter the schedule so each crew sees only what applies to them.”
He explains: “During weekly planning, I generate simplified views for foremen, specifically electrical rough-in in one zone, for example, so they’re not digging through irrelevant tasks.”
Filtering the tasks helps keep everyone on track. “It helps the team see their role in the bigger picture without needing to learn the software,” Bates says. “It also makes it easier for me to track who’s hitting what milestones in real time.”
Use This Checklist to Compare CPM-Based Software Options
Not all project scheduling tools are built with construction workflows in mind. This checklist can help you evaluate different CPM-based software options based on the features that matter most in the field. It’s divided into two sections: functional capabilities (what the tool can do) and technical considerations (how well it fits into your broader system).
Use this checklist to compare tools side by side or to document the key needs for your team:
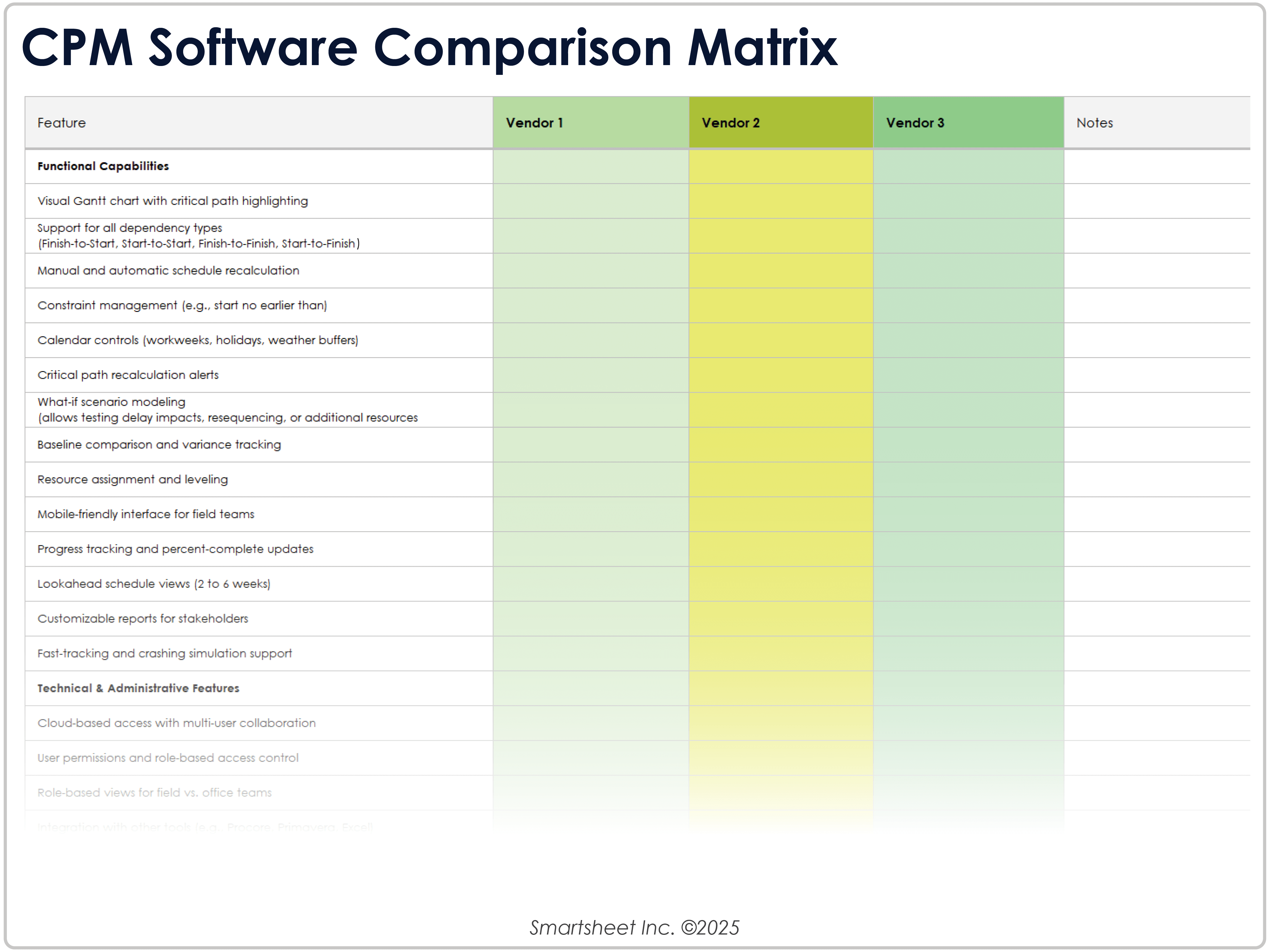
Improve Critical Path Method in Construction with Smartsheet for Construction
From pre-construction to project closeout, keep all stakeholders in the loop with real-time collaboration and automated updates so you can make better, more informed decisions, all while landing your projects on time and within budget.
The Smartsheet platform makes it easy to plan, capture, manage, and report on work from anywhere, helping your team be more effective and get more done. Report on key metrics and get real-time visibility into work as it happens with roll-up reports, dashboards, and automated workflows built to keep your team connected and informed.
When teams have clarity into the work getting done, there’s no telling how much more they can accomplish in the same amount of time. Try Smartsheet for free, today.